Concrete flights, from which stairs are most often built, are distinguished by their increased strength and a very long service life. Metal reinforcement inside structures is a significant reinforcement. Concrete does not crack, does not crumble, is indifferent to moisture and atmospheric influences.
The most relevant are two types of stairs - prefabricated, assembled from pre-cast fragments, and monolithic, which are carried out already in place. Railings, railings and finishing give the structure a complete and presentable look.
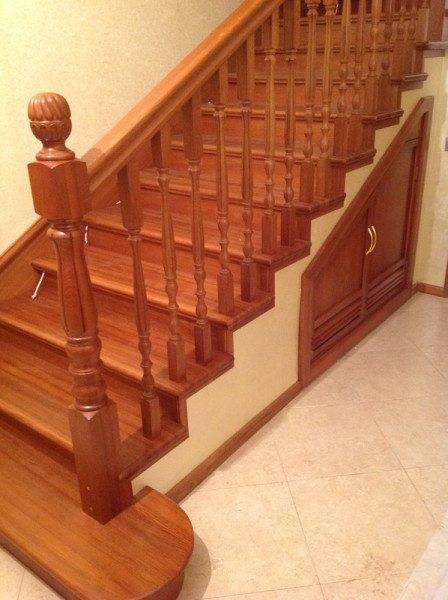
There are many types of finishes - carpet, tiles, stone, wood. Looks very impressive finishing concrete stairs wood, especially if the material is made of valuable species. Oak, larch, ash, beech are the most suitable varieties for these purposes.
The most common mistakes
- Most people believe that the most expensive part of the job is filling concrete stairs... However, facing a concrete staircase with wood will cost the most.
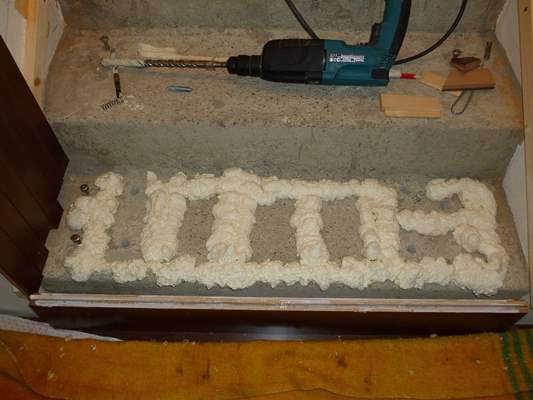
- It is not necessary to fix the solid wood directly on the steps.... This finish will not last long.
- Don't skimp on the thickness of the finishing material... Shields must be 30 mm and more.
- Before final cladding, it is imperative to level the surface and make the veneer.
- It is undesirable to use paint that completely hides the structure of the wood.... You will lose a lot in the appearance of the steps.
- Before sheathing a concrete staircase with wood, be sure to thoroughly clean it of debris and dust, otherwise the adhesion to the glue will be fragile.
- In addition to glue, be sure to use additional fasteners with dowels... Only in this case will the plywood hold firmly.
- Do not save on varnish, buy a moisture-resistant analogue, and the steps should be covered at least three times with dryings.
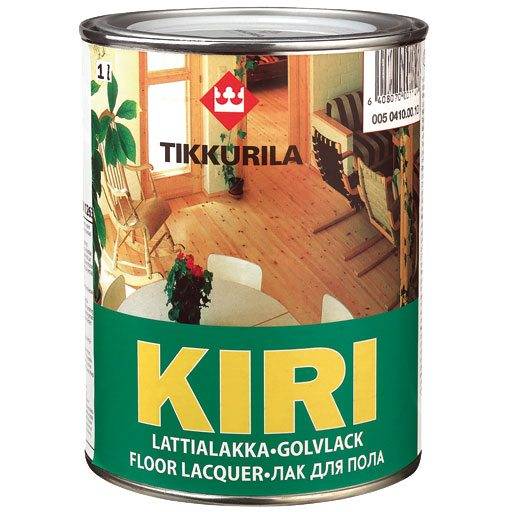
Often they decorate not just built, but old stairs.
Note! Restoration work is undoubtedly a more laborious process, but it will bring the expected effect, the steps will look like new. Doing it yourself is not as difficult as it might seem at first. First you need to prepare all the necessary tools.
Finishing work
First of all, you will need to attend to the availability of tools.
Instruments
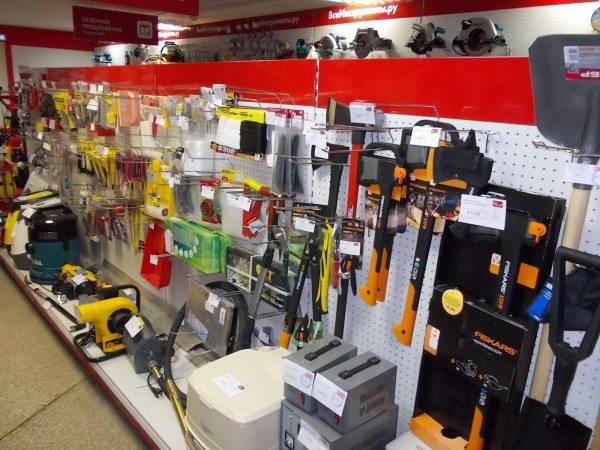
- Electric drill.
- Hammer.
- Electric jigsaw.
- Hacksaw.
- Plumb line and level.
- Grinding machine.
- Milling machine.
- Screwdriver.
Of course, it is worth purchasing in advance the material that suits you, as well as plywood for the substrate, cement and sand for leveling the surface, glue, dowels with screws, as well as top coat or paint.
Installation procedure

- Clean the steps from dust, dilute a solution of sand with cement. It is better to use the M150 brand.
- Make the sizing of the steps by diluting the liquid composition of PVA glue and sand. Let the layer dry for at least 3/5 hours.
- With a spatula, level out all cracks, potholes and irregularities, filling everything with concrete.
- To make the staircase look like a single unit with the wall, mount narrow 10 mm thick veneer plywood strips at the bottom.
- While the mortar dries, pay attention to the risers and treads. To keep your concrete staircase lined with wood, use hardwood. The standard is considered to be the width of the treads at 27/32 cm, and the risers at 15/18 cm. Depending on the characteristics of the staircase, make and mount these elements.

- Using self-tapping screws, fasten the risers and treads as follows. Make a groove in advance with a milling machine, then attach the riser to the tread with the bottom edge flush to the bottom. Drive the upper edge of the tread into the groove from the back. It is convenient to make the groove 2.5 cm wide and 1.4 cm deep.
- You will speed up the process by assembling several tread risers into a single structure. Use a metal corner by attaching it to the side of the tread.
- Additional insulation is a good idea. steps for stairs made of concrete... For this, polyethylene foam with a thickness of 3 mm is perfect. It will protect concrete and wood from harmful influences and create additional sound insulation. Footsteps will be almost inaudible.
- From the bottom riser, concrete stairs are clad with wood. In each workpiece, holes are marked and then drilled, two on each side. Each next part is installed in the groove made, and its even position is controlled.
- It is not recommended to screw self-tapping screws to the end until the entire structure is mounted. Only after checking the final build quality, you can screw in the screws all the way.
- At the very end, the last riser is installed. You can use a metal corner or board.

- Then you can start finishing the railings, if any is planned. Finishing a staircase made of concrete with wood of prestigious species implies a harmonious combination, where the fence is also decorated with the same grade. The easiest is the installation of straight sections, and the most painstaking is the design of "snails", turns and breaks of the line.
- Turns are made by sawing segments at certain angles, gluing them together and screwing them to the base with screws. For a smooth cut, it is best to use a fine-toothed hacksaw. At the end of the work, the joints are putty and then carefully sanded. The color of the putty is matched to the color of the wood.
- The final step is sanding the steps and varnishing.
Note! Purchase a special varnish and read carefully what the instructions for its use recommend. It is advisable to cover in three layers, with intermediate drying.
Try to choose a varnish that favorably emphasizes the structure of the wood. This will give the staircase additional attractiveness and a spectacular appearance.
What kind of wood to choose

Modern wooden stairs on a concrete base must meet all the requirements not only from the aesthetic, but also from the practical point of view. Each owner is free to choose a color, shade and type of wood according to his taste and capabilities.
Quite rare, even exotic wood species imported from afar are often used.
But choosing solid, beautiful and practical wood is not difficult in your region.
- Oak... It can be called a favorite among finishing materials. Affordable, incredibly durable, has pleasant shades and a pronounced pattern on the surface. Anyone who wants to get a respectable appearance of their stairs and a long impeccable service will choose him.
- Larch... There will be no problems with its purchase, and the price will pleasantly surprise, because it is almost two times cheaper than oak, however, it is not inferior to it in quality and external data. Durable and reliable material that will last surprisingly long.
- Ash... It is also cheaper than oak, but even stronger than it. A beautiful pattern on the surface, a pleasant range of colors with variations in shades in the dark and light sides. Given the availability of ash, you will have no problem choosing one.
- Beech... Another worthy contender in the line of leading materials. Homogeneous structure, pleasant color, affordable cost and high quality indicators.
Note! If you are attracted by wood with a beautiful color and texture, but a soft structure, refuse to buy. Linden, pine and similar materials are easy to work with but do not last long.Such a wooden staircase on a concrete base will be inexpensive, but it will quickly lose its attractive appearance and lose its function.
A few tips and tricks
- Pay attention to the matching of the colors of the floor and steps. One should be combined with the other, both in shade and in style.
- In terms of strength, the staircase should not be inferior to the flooring. It would be ideal to use one type of wood in either case.
- The thickness of the finish should be at least 3 cm, if it is thinner, then the coating will not last long.
- The final wood finishing of concrete stairs should be carried out only after complete leveling and cleaning of the surface.
- The gap between the handrails and marches is about 15 cm, however, you should not make it less than 7.5 cm, this is the construction limit. According to fire regulations, a gap of a smaller width is unacceptable, since a fire hose must pass through it.
- Do not build steps with different heights. Such a structure is very difficult to align, and it is not recommended to use adhesives and putty compounds for these purposes. Deviations in the heights of the riser and tread up to 1 cm are considered permissible. To level the heights, it is advisable to use concrete mixtures with additional reinforcement of the steps.
- Even beautiful wooden stairs on low quality concrete will not last long. The cement will begin to deteriorate under the coating, which will render the entire structure unusable.
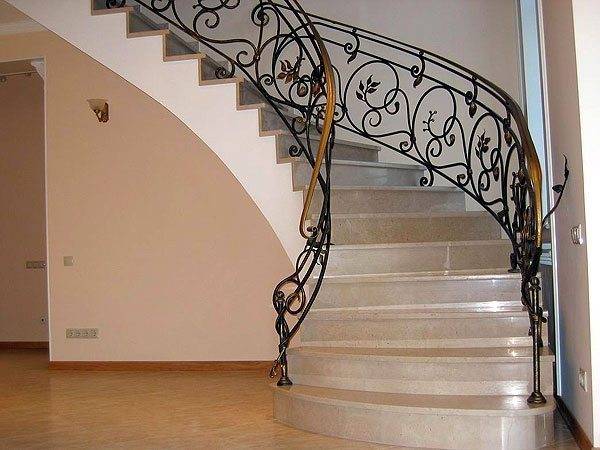
- Wood-trimmed staircases look very beautiful in conjunction with wrought iron railings, as well as glass and chrome elements. Crossbars, balusters, steps and railings should preferably be in the same style and color.
- It is advisable to carry out finishing work after the main repairs have been completed. In general, sheathing of concrete stairs with wood will not create a lot of dirt; with proper work, there will be a minimum of garbage.
- If possible, use the services of specialists. At the very least, the designer's advice will do you good, he will advise a competent solution specifically for your interior. Hired workers with the skills and the necessary tools will make the cladding much faster than non-professionals.
Output

If you know how to properly sheathe a concrete staircase with wood, then you can easily decorate your interior on your own. But with the slightest uncertainty or employment, do not take up work, it is better to carve out a little money from the budget, and let competent specialists please you with the result.
In the video presented in this article, you will find additional information on this topic.