disadvantages
Arbolit has many advantages, a little less - disadvantages. The main disadvantage is the high risks of acquiring handicraft modules. The fact is that high-quality blocks are produced at large industrial enterprises that cannot be found in the region.
Such manufacturers do not think about the performance of the building materials produced. They make modules by disrupting the manufacturing process. As a result, they sell wood concrete, the technical characteristics of which are significantly lower than those stated.
Another disadvantage is the low density of the material. On the one hand, this is a positive moment, since the load on the foundation is reduced, and on the other, such blocks cannot be used for the construction of multi-storey structures.
There are a number of other disadvantages of this material.
- Dimensional deviations. Finished blocks can vary significantly in terms of standard sizes prescribed by the regulations. Sometimes, due to a mismatch in the parameters, builders have to increase the thickness of the seams. This leads to the formation of "cold bridges" and freezing of the seams in the cold.
- Biological instability. Wood concrete blocks are products that rodents "love". Mice and rats make numerous burrows and passages in them, which significantly reduces the service life of the building. To protect the structure from such pests, you will need to make a concrete basement. And this is additional monetary waste on building materials and hiring a construction team.
- The need for a decorative facade finish. Arbolit is an aesthetically unattractive building material (if we are not talking about products with cladding). To improve the appearance of the building, you cannot do without finishing. It will entail the costs of purchasing cladding and hiring labor.
- Poor resistance to high humidity. Arbolite blocks are capable of accumulating moisture, which over time destroys the material. In order for the wood concrete structure to last as long as possible, you need to make a foundation base with a good waterproofing shell and plaster the outer part of the wall.
- High price. Here we are not talking about blocks of low quality, handicraft production. Products that meet GOST standards are not cheap. Their price is about 1.5 times higher compared to the cost of aerated concrete or foam block.
Some disadvantages of wood concrete are associated with a violation of the technology of its production or with the use of low-quality components. In order not to purchase blocks unsuitable for construction, you need to heed some recommendations.
Manufacturing technology
The production of wood concrete in blocks at large enterprises is automated. The manufacturing process includes several stages, which are described below.
- Loading the organic filler into the dispenser. The dosing device is fixed to a hoist that delivers the component to the mixing equipment container.
- Loading of chemical reagents.
- Adding a certain grade of Portland cement.
- Thorough mixing of the components of the mixture until a homogeneous mass is obtained. The resulting solution is sent to a vibrating table with a vibrocompression device.
- Leveling the mass in the forms. At this stage, the products are compressed due to the use of a press. If it is necessary to obtain blocks of non-standard shapes, special plates are manually inserted into the cells. The result is triangular or trapezoidal products.
- Sending blocks to drying chambers.The temperature at which products must be dried is not regulated by GOST. However, materials may be left in the cell for a maximum of 24 hours.
Particular attention should be paid here to wood chips. Of all types of wood, conifers such as fir or pine will be preferable.
The presence of bark or needles should not be more than 5% in relation to the total mass.
When creating blocks at home, not every builder may have chemical additives on hand. Without them, the adhesion process will be significantly difficult, and the hardening time of the products will also increase (sometimes it takes several weeks to dry). Self-production of high quality material with your own hands is unlikely. Most often, at home, block products are created for the construction of structures with low operational requirements.
Arbolit pros and cons.
Our time is characterized not only by an abundance of construction technologies, but also by a large selection of materials that can be used to build houses for permanent residence. Several decades ago, private developers had to choose between two materials. They were choosing between brick and wood. Depending on their financial capabilities, they purchased the most suitable material.
In the conditions of existing reality, the choice is incredibly huge. In addition to wood, developers can choose a foam block or opt for aerated concrete. In addition, houses can be built from materials based on expanded clay.
Recently, such material as arbolite began to gain popularity. We will consider the pros and cons of this material.
Arbolite composition
Pros of wood concrete.
So, wood concrete, it is sawdust concrete (chip concrete) or wood concrete. Blocks made of it are inexpensive and at the same time have a large set of performance characteristics. Many people who want to build an eco-friendly home make a choice in favor of this material. Despite the fact that blocks of wood concrete for the most part consist of wood chips, they nevertheless please with their reliability and durability.
Arbolite textured
The properties of this material largely determined the situation when many developers prefer it in its favor. By building a house from this material, you can get a reliable structure that will not have any effect on health and at the same time will be inexpensive. Many people do not like the gray look of such buildings. However, this problem can be easily solved if you carry out the finishing work of the facade walls using modern materials, which are offered in a wide range in hardware stores.
Arbolite textured
It must be understood that none of the building materials offered at the moment are free from disadvantages. Although wood concrete blocks have many advantages, nevertheless, this unique material also has disadvantages. If you are seriously considering wood concrete as a material for the construction of your new home, then, of course, you should learn about the main disadvantages of this material.
Cons of wood concrete. Disadvantages of the material.
One of its main disadvantages is that it does not tolerate moisture. Therefore, when erecting a structure, the walls of rooms in which high humidity will be present must be made of another more moisture-resistant material, but not wood concrete.
The thing is that this material is made from wood chips, and everyone knows that wood does not tolerate moisture well. Therefore, it is worth abandoning the idea of using this material in rooms with high humidity. If you neglect this recommendation and, for example, make walls of this material in the bathroom, then you will face certain problems. The material will absorb moisture, and ultimately this will lead to the fact that its performance is noticeably reduced. As a result, the service life of the building will be significantly reduced.
However, we note that it is possible to eliminate this disadvantage. To do this, you can finish the walls of wood concrete blocks using modern finishing materials. An excellent option would be to use plaster.
Another disadvantage that you should be aware of is that wood concrete blocks have poor resistance to gases with an aggressive environment.
In addition, this building material has other disadvantages. The basement of the house, which is built of wood concrete blocks, must be additionally finished. The main goal of this work is to achieve maximum dryness. In this case, you can ensure a long service life of the structure.
It should not be forgotten that wood concrete blocks are 90% made of wood. For this reason, it is necessary to regularly monitor the condition of the base. In winter, it is necessary to regularly inspect it and ensure effective drainage, and also make sure that the basement is free of snow.
Another drawback of the material is that such blocks do not have ideal geometry. However, we note that this drawback has no effect on the speed of construction work. But it is still necessary, when performing masonry, to make a choice in favor of a solution based on cement and sand. In this case, the irregularities that the blocks used during the construction have will be leveled by the solution.
No. 6. What to consider when choosing wood concrete?
There are a lot of manufacturers of wood concrete blocks today, we will not single out someone specifically, since there are worthy companies in each region and it takes a very long time to list them. On the other hand, everywhere there are a lot of handicraft industries that are trying to sell frankly bad goods at a higher price, and even a quality certificate is not always a guarantee of actual quality, because we all know how documents are sometimes made. It is best to visit the production site, evaluate the technology and quality of the blocks with your own eyes. What are the criteria for checking and how to understand that the product is of poor quality?
First of all, attention must be paid to wood chips. GOST regulates its parameters 40/10/5, i.e.
it should be rectangular and large enough, in one block there should be chips of approximately the same size. Square chips will not provide a normal bond, and small sawdust will not provide high-quality thermal insulation. Machines that make oblong chips are many times more expensive than units that make square chips, the more the latter can be obtained for free at almost any woodworking industry. Better if pine chips were used.
Externally, the wood concrete block cannot be absolutely smooth. On the contrary, the ideal surface is typical for blocks made with sawdust and square chips, and the smooth surfaces of such blocks confuse buyers.
All sides of the block must be the same. If one end of the product is smooth, and the rest are very different from it, then the production technology was violated and the cement flowed down. This block is not suitable for construction.
There should be no white plaque on the blocks (evidence of adding glue or pouring down milk), chips should not be picked out by hand (an indicator of poor adhesion).
The geometry of the blocks must be observed, the maximum permissible deviation is 5 mm.
Cement should be used grade M500.
Give preference to blocks produced by vibratory pressing - manual ramming does not allow you to achieve the required strength. It is best if the blocks are kept in molds for 24 hours. If instant stripping is used, the geometry of the blocks can be significantly disrupted.
# 1. Wood concrete composition
Arbolit is one of the varieties of lightweight concrete. The name of the material traces French roots: arbre is translated from French as "tree".If you know this fact alone, you can guess what basic materials are part of the wood concrete. So this:
- wood chips (up to 80-90% of the volume);
- cement;
- water;
- chemical additives to improve the strength and increase the adhesion of chips to cement.
It is clear that the characteristics of the finished material depend on the quality of raw materials. Since the chips in the wood concrete block are the most, the greatest importance is given to it. It is chips that should be included in the composition - not sawdust, hay, tyrsa or shavings (otherwise it will already be sawdust concrete). The strength of the material depends on the caliber of the chips. According to the standards, the length of chips can be up to 40 mm, width - 5-10 mm, thickness - 3-5 mm. It is desirable that the block contains only chips without any impurities, although a small amount of bark (up to 10%) practically does not affect the strength of the products. The type of wood is not so important, but usually pine or spruce is used, and larch is used much less often, since more additives will be required due to the nature of the wood.
Cement is used not lower than the M400 brand, but since it has the peculiarity of quickly losing strength properties during storage, it is better to use M500 cement in the production of structural wood concrete blocks.
One cannot do without chemical additives in the production of wood concrete - the sugar contained in the wood is to blame, which impede normal adhesion. Therefore, well-dried wood is used in production, but this does not help either. The surface of the chips is mineralized with lime, calcium chloride, water glass or sulphate alumina.
The ratio of the components is regulated by GOST. If, for example, the water content is exceeded, then at the exit you can get a block of insufficient strength, and there will be more problems with its manufacture.
Arbolite is produced in several forms:
- masonry blocks;
- hollow blocks;
- thermal insulation boards;
- panels;
- mortar for creating monolithic structures and pouring in place (like expanded clay concrete and polystyrene concrete).
Since blocks of wood concrete have found the greatest use, today they are meant by wood concrete. As a rule, they are made with dimensions of 500 * 250 * 200 mm, but products with other parameters can be found.
Applications and form of release
Lightweight concrete based on organic aggregates and building materials made from it are used for the construction of private low-rise houses and other buildings, the load-bearing walls of which are not subjected to high compressive loads. According to GOST R 54854-2011, wood concrete is used in the following areas:
- as monolithic thermal insulation and sound insulation of roofs, attics, ceilings, three-layer panels, floor slabs and coverings, floors;
- for the construction of load-bearing, external walls and internal partitions;
- for precast monolithic walls;
- as elements of permanent formwork.
The concrete grade depends on the loads tested in the structure. The outer and inner sides of the block must have a finishing layer. This will ensure their protection from excessive moisture and subsequent destruction.
There are several varieties of wood concrete. These include:
- Large building blocks. They are used for the construction of walls in low-rise buildings, outbuildings and industrial facilities. The most common block size is 500 × 300 × 200mm.
- Roof and wall covering slabs. They are used as a heat-insulating and sound-insulating outer covering.
- Liquid mixture or monolithic wood concrete. It is used for casting formwork during the construction of monolithic parts of the structure.
Arbolite block
Slabs
The production of organic concrete is carried out in accordance with the requirements of SP 63.13330.2012 and SN 549-82. The size of the building blocks has no established standard dimensions. It is regulated by the internal regulations of the company and may differ from manufacturer to manufacturer.
Attention! In the process of forming parts or pouring a liquid mixture, the recommended temperature should be at least 15C.
The main technical characteristics of this material
Arbolite must meet the following quality indicators:
- Average density (kg / m3). D300-D500 grades are installed for the thermal insulation material. Structural wood concrete grades - from D500 to D900.
- Compressive strength. Concrete corresponds to different strength classes (B0.35, 0.75 - for one-story buildings and B1.5, 2.5, 3.5 - for two-story buildings). Arbolit has brands M2.5, M3.5, M5, M10. Depending on this indicator, the type and functional purpose of the material is determined.
- Thermal conductivity. This indicator allows you to determine the required wall thickness. Since wood concrete material has a low coefficient of thermal conductivity, this allows it to be used in construction in areas with cold climates. GOST R 54854-2011 establishes thermal conductivity coefficients (W / (m K)), depending on the grade of concrete (D300 - 0.07, D500 - 0.95, D800 - 0.17).
- Moisture absorption and vapor permeability. These indicators are regulated by the standards of GOST 4.212-80. The water absorption coefficient for wood concrete is 75 - 85%, vapor permeability - up to 35%.
- Frost resistance. This coefficient shows the resistance of the material to the effects of variable cycles of freezing and thawing. For structural and heat-insulating wood concrete, frost resistance grades F15, F25, F35, F50 have been established.
- Shrinkage. Tests show that lightweight organic concrete is subject to a minimum shrinkage of 0.8%.
- Fire resistance. This indicator is subject to several fire safety requirements. Grades from D400 must correspond to flammability group G1, toxicity of combustion products T1, flammability B1 (GOST 30244, 12.1.044, 30402). In accordance with these indicators, wood concrete is a slow-combustible material, with a small amount of smoke emitted.
- Soundproofing. Thermal insulating wood concrete materials have high sound insulation properties, with a sound absorption coefficient of up to 0.6 dB.
The properties of different types of wood concrete depend on the grade of cement used, chemical additives, production technology and the material that protects the outer parts of the wood concrete blocks.
Quality control tests
Before releasing wood concrete for sale, the manufacturer conducts a series of tests. Quality control includes the following tests:
- determination of the granulometric composition of the aggregate;
- assessment of all quality indicators of the material in accordance with GOST 10181 (thermal conductivity, strength, vapor permeability, fire safety, etc.);
- verification of radiation indicators and compliance with sanitary and hygienic requirements.
Based on the results of the check, the material receives certificates of conformity and is sent for implementation. Certificates confirm the safety of wood concrete for human health.
DIY block making
Blocks can be produced by yourself. However, you should be prepared that the result does not always meet expectations. With manual ramming, it is difficult to achieve the required material strength.
Handcrafted blocks
The most important thing when making blocks with your own hands is to stock up on organic filler. It is convenient when there is an opportunity to agree on its delivery to a woodworking enterprise. Installing a crusher on your farm for the production of a small amount of products is not very justified.
For the work process, you will need a concrete mixer and split forms.
Detachable form
Better if they are metal. It is recommended to overlay wooden structures with linoleum from the inside. This will make it easier to retrieve finished products.
Video - Form for the preparation of wood concrete blocks
Block production technology is not complicated.
Step 1. Preparing the filler. It must be free of foreign matter.
Step 2.The filler is loaded into the concrete mixer, the unit turns on.
Step 4. Water mixed with calcium chloride is poured into a working mixer, additives are added. The chips should be evenly saturated with water and darken.
Step 5. Cement is added. The proportions of the components (by weight): 1 part of water, 6 parts of wood chips and 1 part of cement. Calcium chloride needs 2% of the mass of cement. Mixed until homogeneous (there should be no chips left that are not covered with cement), the mass should be crumbly, but plastic.
Video - Kneading wood concrete
Step 6. The mass is discharged from the mixer.
A homogeneous mixture prepared in a concrete mixer
Step 7. For the production of blocks, metal molds are used, the removable bottom of which is covered with a film so that the concrete does not stick to the base. It is more convenient when the matrices can be disassembled. This makes it easier to remove the block.
The bottom is covered with a foil to obtain blocks with a better surface
Step 8. The mixture is poured into the mold in layers. Each layer is carefully rammed.
Layer-by-layer form filling and further ramming
The form is covered with a lid
Tamping under its own weight
Step 9. The next day, the block is removed and sent to dry. In this case, the product should be covered with polyethylene.
Unshaped block
Drying of products is carried out on a boardwalk under a film
Component composition and standard parameters of wood concrete
Arbolite mixture is a very multicomponent, special mixture, consisting of a complex of additives and special additives:
1. Finely chopped hardwood (birch, poplar, aspen, etc.) and coniferous (fir, pine, spruce, cedar, etc.) species. All wood material must meet the parameters in a dry state:
- the size of the elements is no more than 3.3 cm in length, 1.3 cm in width and 0.7 cm in height;
- the proportion of bark is not more than 11.5%, and needles and leaves are less than 4.8%;
- a complete absence of all kinds of additives (sand, stones, clay, kidney, etc.) is required;
- of course, the presence of fungi, rot, mold, snow, frost, etc. is unacceptable.
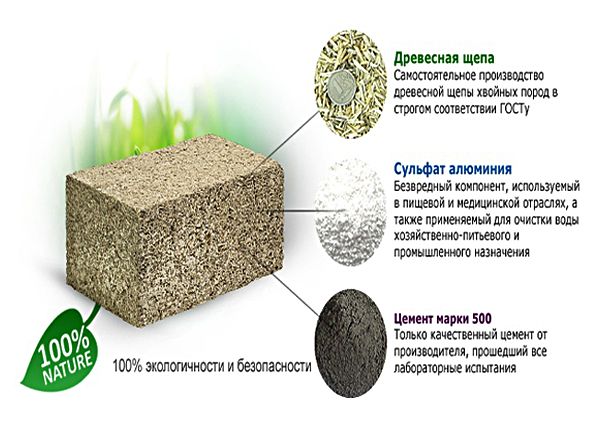
3. Crushed filler (ballast) - very fine sand is used to increase the non-essential strength of the wood concrete material.
4. Chemical-synthetic additives - significantly improve the quality of the cross-stone construction mixture. These substances include:
- antiseptics and herbicides;
- stimulants of hardening;
- anti-corrosion additives for wood concrete with iron reinforcement;
- stabilizers and regulators of the porosity of the structure.

Important!
To prevent bacterial decomposition and fungal fermentation, add calcium chloride, aluminum sulfate, liquid glass, etc. to the initial mixture!
5. The existing building codes (standards) for wood concrete define the following standard coefficients of strength and compression:
- thermal insulation standards - Bm0.50; Bm0.750;
- design parameters - Vm10; Bm1.50; BM20; Bm2.50; Bm30; Bm3.50.
6. Premium concrete material has a very significant thermal conductivity and strength.
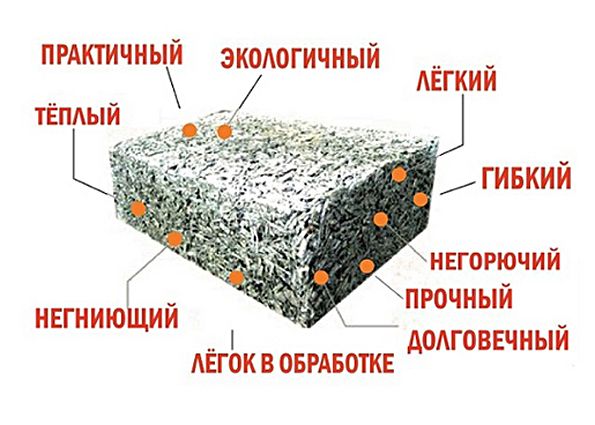
Quality product criteria
The choice of wood concrete is a responsible process, since the service life of the future structure, as well as the microclimate inside it, will largely depend on it.
When buying a material, experienced builders advise, first of all, to pay attention to its cost. It is unlikely that the manufacturer will work to his own detriment and sell high-quality wood concrete blocks below their market price.
When choosing wood concrete, it is important to visually evaluate it. Below are the quality indicators of such material
- Uniformity of composition. If the wood concrete mixture was heterogeneous, the finished blocks will delaminate over time. According to the regulations, the stratification rate should be less than 10%.
- Correct geometric shape. Its violations are observed when the storage conditions of finished products or production technology are not observed.
- Uniform gray color.The uneven color of the blocks or foreign inclusions indicate the low quality of the products. For example, the presence of green or brown shades is a sign of underdried products. It is worth considering that materials may have various inclusions (straw, sawdust, needles, bark), but not more than 5%.
- Chips of the same size (the presence of particles with sizes exceeding the established norms is unacceptable). Too large wood fractions are unable to be completely saturated with chemical reagents. Because of this, they do not mix well with concrete and reduce the strength of the finished building material.
To be sure of the quality of wood concrete, you should agree with the manufacturer about the possibility of laboratory testing of selected samples of material from a released batch.
Output
Having added and weighed all the pros and cons of this building material, and taking into account the reviews about the houses made of wood concrete, the following conclusions can be drawn. Arbolit is perfect for building a house:
- in a noisy area;
- in regions with a predominance of low temperatures and dry climate;
- with a preference for reliable and environmentally friendly materials.
But at the same time, it is worth using other technologies when building a house in regions with a high moisture content in the soil and atmosphere, since wood concrete absorbs moisture quite strongly.
2. Victor Nikonorovich (Moscow region)
I chose wood concrete for reasons of resistance to deformation. The fact is that we live in the suburbs. The soil in our area is of the heaving type, i.e. subject to frost heaving. The builders advised the use of wood concrete blocks. Arguing this by the fact that arbolite is able to compensate for the movement of the ground.
The foundation is tape. The house, built and finished according to all the rules (as the builders assured), has been in operation for 7 years. No cracks are visible yet. And what is especially pleasant, in comparison with a neighbor who has a brick house of a similar square with foam insulation, one third less money is spent on heating.
3. Nikolay (Tyumen)
Newly built house made of wood concrete blocks. The work was carried out on its own. There is no internal and external decoration yet, there are bare walls and a warm contour (windows, doors), after the installation of which, after a while, an unpleasant smell appeared. Although, I was waiting for the promised microclimate and the smell of wood.
In fact, you can clearly smell some kind of chemistry. Has consulted with experts from the construction company. It turned out that the additives that are part of the wood concrete are the source of this unpleasant odor.
The question of whether the finish will eliminate it or it will fade over time remains open. The inner walls, just in case, I put in aerated concrete. There are no complaints about him.
4. Peter Viktorovich (Surgut)
A house made of wood concrete keeps heat for a long time. Personally, I think this is the ideal material for our Siberian frosts. Yes, the material is blown through, this was especially noticeable at the construction stage, immediately after the installation of windows and doors. Further finishing eliminated drafts. So, with the right finishing, this is rather an advantage than a disadvantage, since it provides the necessary ventilation in the house.
5.Sergey (Voronezh)
Many insulation materials (polystyrene, expanded polystyrene, mineral wool) contain dangerous formaldehyde, which is constantly released and is a carcinogen. I think the environmental friendliness of wood concrete is an excellent recommendation for its use. P.S. my house is under construction.
6. Anatoly (Rostov-on-Don)
My review is negative, because working with arbolite is a complete punishment! Dimensional deviations reach 10-20 mm. As stated by the manufacturer, this is permissible according to some kind of GOST. It is very difficult to provide the necessary evenness of the wall surface. Its only advantage is that it is easy to cut and fit. I have to invite builders to finish the work, although I drove out the change house from foam concrete myself without any problems.
7. Konstantin (St. Petersburg)
The house is cold.We have been living in an arbolite house for the third year. Initially, insulation was not planned, however, as practice has shown, one cannot do without it.
We searched on the Internet why it is cold in a house made of wood concrete blocks, there are many opinions, one of the suitable versions is that this is due to the use of a structural block, and not a heat-insulating one. But we were building a house with 2 floors with an attic! We needed a durable material and warm.
An excess of the cement content in the block was also named as a reason, which also reduces the wall's ability to retain heat. It is generally unrealistic to check it visually. As a result, we tried to make it "cheap and cheerful", but in fact we will have to overpay for additional insulation.
8. Arthur (Novosibirsk)
I bought wood concrete with a margin. After a year of storage in a garage without packaging, I decided to use it for the construction of a bathhouse. Sheathed the walls with insulation and waterproofing film. He left a ventilation gap so that the wood paneling did not deteriorate. I have been using the bathhouse for the second year. Outside, finishing with 10 mm plaster (the masonry is crooked, I had to apply a lot of plaster). So far, I am satisfied with both the house and the bath.
9. "Inquisitive 74" (Ufa)
While choosing wood concrete, I noticed that there are blocks with large chips, and there are blocks with small ones - almost with sawdust. The first is wood concrete, the second is sawdust concrete
According to tests, the thermal conductivity of wood concrete blocks is higher due to the lower amount of binder.