Formwork lubricants
The main purpose of using various types of formwork lubricant is to prevent strong adhesion of the concrete mixture and the material from which the mold is made. This is necessary to facilitate the dismantling of the removable formwork, carried out after complete fixation of the concrete. Thanks to the use of lubricants, the geometric shape of the foundation is preserved, and its surface becomes as flat as possible. This leads to a reduction in the cost of finishing, achieving the quality and durability of the base of the building.
Any formwork material other than plastic requires lubrication
A set of requirements is imposed on lubricants aimed at maximizing construction efficiency:
- the grease should not leave oily stains on concrete surfaces. The exceptions are those cases when concrete structures are covered with earth, covered with waterproofing;
- the substance should not affect the strength, composition, density of concrete;
- the composition of the lubricant should not contain volatile components that negatively affect human health;
- the product should be kept on vertical or horizontal surfaces for at least 24 hours.
The action of lubricants is based on the presence of fatty acids in their composition, which form a protective film on the treated surface. As a result, the removable mold is easily dismantled and the concrete retains a high surface quality.
Emulsol
For processing forms, oil mixtures "Emulsol EKS-A" and "Emulsol IM" are often used. They provide a flat concrete surface after mold removal, without pores and holes, and easy dismantling of the device. The composition of "Emulsol" includes corrosion inhibitors, mineral oils, emulsifiers. Due to the proportional ratio of substances, the lubricant has a low fire hazard and does not interact with additives in the concrete mixture.
Concrete surface with and without lubricant
"Emulsol" provides water-repellent properties, which prevents moisture from affecting the base of the foundation. The product is applied using a paint sprayer or brush. The first option is optimal for treating large surfaces, and the brush is convenient for applying the product to a small area.
Mold processing oil
The ability to form a thin film on surfaces is possessed by products containing mineral oils. Among those in demand are "TiraLux" and "TiraMin". They are not diluted with water, have a transparent color with a slight yellowness, do not affect the shade of concrete. Application involves the use of a special spray or spray gun. On small surfaces, a brush can be used, but the thickness of the grease layer should not be more than 0.3 mm.
Manufacturers produce grease in a variety of containers
Mineral oil products are safe for human health and can be used in the construction of residential buildings. All quality products for formwork processing are characterized by a low level of fire hazard.
Water based products
The lubricant, which contains oils, forms a thin film that provides waterproofing and concrete protection. There are simpler substances in the form of a dry powder that are dissolved in water. They have a low cost, they are applied in the same way as oils, that is, by a spray. The main difference between water-based products is their low degree of effectiveness and the fact that they are not used for processing formwork from rough materials, such as boards.
Spraying is the most efficient formwork lubrication method
Water-based products include powdery components that dissolve well in water. It is easy to prepare the solution yourself by studying the instructions on the package.
Video: Spray Lubrication
Formwork made of different materials differ in installation technology, technical characteristics and other properties.
Before building a building, it is important to determine the best material for the forms used, because the quality of the concrete structure will depend on this.
We build the formwork
The assembly of the strip foundation formwork is carried out after the soil has been compacted and the plane has been leveled. For the installation of the formwork, any suitable material that you have is suitable. If you are assembling removable formwork, then the best option would be a wooden planed board. Formwork under strip foundation from such material can be easily removed after the concrete has hardened. For arranging a fixed type of formwork, expanded polystyrene is well suited.
When choosing a board for assembling formwork panels, it is necessary to take into account the pressure that will be created as concrete is poured into the trench. Shields are made a little wider than the depth of the trench, and their number depends on the length of the pit. Along the entire perimeter, at the same distance from each other, wooden pegs are driven in, on which the prepared shields are then installed. To give the structure strength and reliability, it should be strengthened with spacers and lintels, which are made of the same material as the formwork itself.
When the formwork is ready, it is measured out with a level and the construction of the strip foundation is started according to the following technology: roofing material is laid on top, a reinforcing cage is mounted inside the trench and poured with concrete. After 6-7 days, the strip foundation is gaining its qualities, after which you can continue construction work.
The manufacture of formwork for a strip foundation, as well as the construction of the base itself, is a rather laborious process, but you can cope with it yourself. It is enough to have a tool, a great desire to build something on your own and adhere to a certain technology, and then you will succeed!
How to properly assemble formwork for a strip foundation made of wood: step-by-step installation
When erecting wooden formwork, it is best to resort to the use of edged boards or wide plywood. Further, from these materials, it is necessary to assemble the shields of the required dimensions. After that, you need to arrange grooves on their outer contours to combine the elements with each other. All joints should be processed with a sealant or polyurethane foam. The moisture content of the wood used should not be high. In height, the shields made should not exceed the level of the foundation tape by more than 50-70 mm. After carrying out the preparatory work and purchasing the necessary materials, you can proceed to the construction of the formwork itself. Actions must be performed as follows:
- First of all, it is required to install ready-made shields from the outside of the trench and strengthen them with braces, where soil or reinforced pillars act as the main fixing component. After that, it is necessary to nail the braces to the boards, and then install them with a step of at least 1 m between them.The minimum allowable distance reaches 30 cm for thick bases.
- At the next stage, using nails or corners, it is required to fix the jumpers of a fixed length. Their maximum length should not exceed the width of the tape of the base being erected.
- In the same way, the installation of the inner part of the formwork should be carried out and tightened using clamps, nails or other fasteners.
- Then you need to make sure that all the shields are placed vertically and horizontally. The slope angle is not more than 3 °.In addition, they should be free of deflections or bends. The regulation of the shields must be done by means of rails, a level or a building hydro level. For plywood, permissible deviations can be up to 0.2 cm, and for wooden boards - up to 0.3 cm.
- Then you can make the preparation and pouring of concrete solution. After it has completely solidified, the formwork can be dismantled, which, if necessary, can be reused.
Note! Before pouring the concrete solution, it is necessary to make passes for communications, for making which round sleeves are used.
The correct placement of the panels of the structure can also be adjusted by means of threads and wire rags, as well as fasteners of a fixed type. Giving preference to non-separable formwork, it is recommended to fix wood planks on the inside of expanded polystyrene, in which it is necessary to install strong hooks and flexibly combine the reinforcement. In this way, the hooks will tighten both surfaces of the formwork and fix them in the required position.
Upon completion of the installation, the inside of the structure must be covered in several layers with roofing material, which prevents the flow of concrete mortar, and also provides waterproofing of the tape. The waterproofing material must be laid down from the angles of the slope near the sand cushion, thereby avoiding the rupture of the coating during the pouring of the mixture. It is best to bend the upper part of the roofing material over the upper edge of the formwork, fix it with clamps, screws or using a stapler. In this case, the sheet is able to withstand the load that occurs when pouring concrete from an automobile concrete mixer.
What is needed to prepare the poured mixture
Pay attention to the quality of building materials when purchasing
- Ready concrete. Grades from M100 to M300 are used. The choice is made based on the upcoming operating conditions when designing.
- Cement. Use M300, 400, 450. When preparing a solution with your own hands, depending on the brand of the mixture obtained, the amount will be from 170 to 320 kg per m³. It must be dry, free from compacted grains (poor storage), free-flowing.
- Sand. Quarry mining, no clay, dust, debris. In the presence of such inclusions, it is necessary to sift, rinse. The proportions are in the range of 4.6 ÷ 1.9 to cement, depending on the grade of concrete.
- Water. Plumbing. In other sources, there may be an increased content of salts, acids, sulfates, leading to a slow destruction of the binder components of the monolith.
- Crushed stone. Add in a ratio of 7 ÷ 3.7 to cement, similar to sand. Sometimes they try to replace it with slag, construction waste. This reduces the ability to withstand moisture, temperature changes. It is better to use expanded clay with a strength of 1.2 to 1.6 MPa.
We recommend watching a video on how to choose the right concrete grade.
It is necessary to determine the numerical values of the ingredients by multiplying the geometric dimensions of the foundation. Each grade of concrete allows you to calculate the measure of the constituents from the proportion. On construction sites there is a calculator that calculates the amount of mortar, reinforcement and formwork.
The solidity of spreading in a given shape is achieved by subsequent tamping. A vibrating screed helps to effectively carry out the work of removing air. With a large layer thickness - a deep vibrator. One immersion of the rod covers with its action in a radius of 0.5-0.9 m. It is processed for 1-2 minutes until water gloss appears on the surface.
General principles and features of the installation of permanent formwork
The construction of the foundation using the technological technique of permanent formwork is not difficult, although it consists of several successive stages, which are characterized by specific features. Let's consider them in detail:
1. Preparation of land at the construction site
The created monolithic foundation, in direct dependence on the functional purpose of the building under construction, can be directly laid on the leveled ground or in a dug trench. Although, regardless of the chosen method, during installation, a sand and gravel "cushion" with a thickness of more than 11.0 cm should be placed under the lower surface of the foundation. Such a carefully compacted layer effectively compensates for the expansion of the soil and small displacements of its layers with changes in temperature or changes in the level of groundwater.
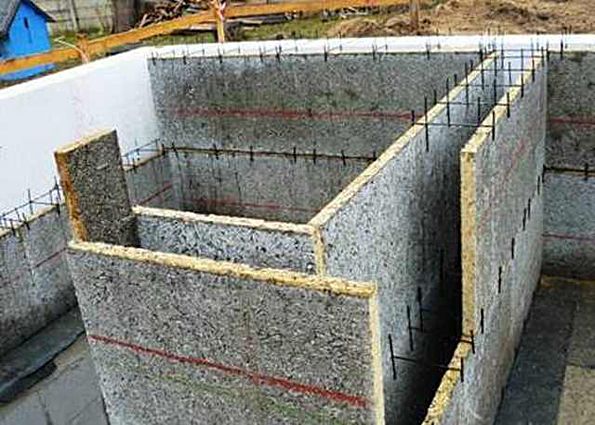
2. Installation of the structure of the permanent formwork
Since the design process (design and installation) of permanent formwork is very simple, especially from expanded polystyrene material, it is accessible even to untrained workers. The main thing is that the employee has minimal skills in construction and technological production.
Fixed formwork made of lightweight materials is installed according to the principle of a children's designer or classic brickwork.
Sets of parts for creating such formwork from well-known manufacturers contain expanded polystyrene sheets equipped with special ridges and grooves on the end surfaces. This is necessary for tight, high-quality adhesion and fixation of the sheets.
Nuance! Certain types of permanent formwork contain a metal reinforcing grid in their structure, which perfectly replaces the internal reinforcing frame. In addition, modifications are produced in which the formwork consists of a combination of wood, glass magnesite and concrete!

Types of shields
The set of panel formwork includes the following types of panels:
- universal linear;
- corner;
- articulated,
- for columns.
The most popular type is linear formwork panels, they are universal and interchangeable. Using universal formwork panels, it is possible to create various modular structures, since the elements can be joined both vertically and horizontally.
Corner and hinged formwork panels are used to form the corners of the structure. Moreover, the hinged version is more convenient, since it allows you to form both external and internal corners.
The hinge element consists of two profile parts, joined by means of a hinge joint. The combination of hinged formwork elements of different sizes allows you to collect forms located at any angle to each other. In addition, the formwork elements differ in the material of manufacture. The most common designs are:
- wood and wood-metal;
- metal.
Less commonly, plastic elements are used, although plastic systems have recently become more and more popular.
Wood and wood-metal
Wooden panel formwork is an option that is most common in private construction. It's all about the availability and relative cheapness of the material. For the manufacture of wooden formwork, planed boards and laminated plywood are used.
For assembly, use boards with a width of 150-300 mm and a thickness of 20-25 mm. The dimensions of the panels to be assembled depend on the dimensions of the structure that is planned to be built.
But, as a rule, the elements are small, so the formwork can be assembled manually without the use of lifting equipment. For larger objects, wood-metal panels can be used; they have a metal frame and a main part made of film faced plywood.
Wood-metal formwork systems are reusable and can withstand up to 200 use cycles.
Metallic
In professional construction, metal formwork is often used, its advantages:
- the ability to manufacture a perfectly flat and smooth surface;
- fast assembly and disassembly;
- high strength and rigidity of structures;
- multiple use, kits can withstand 500 cycles or more.
A significant drawback is the high cost of metal kits, so the option is optimal only for professional construction.
In private construction, as well as for the construction of structures with complex geometry, it is often the small-panel formwork that is used. Large shields are used for casting dimensional elements of simple geometric shapes. The metal formwork is represented by steel or aluminum panels. The former are more durable, the latter is lightweight.
Formwork materials
For the manufacture of formwork for tape a variety of materials are used for the foundation. However, when choosing, you need to take into account the basic requirements for formwork systems, it is they who determine the need to use certain materials:
- Flexural strength. The permissible deflection of the boards when pouring the concrete mixture should not exceed 2 m.
- Rigidity. The elements from which the structure is assembled must be qualitatively interconnected.
- The smoothness of the shields. Level differences on the board surfaces should not exceed 2 mm. The same requirements apply to the junction points of the shields.
- Accuracy of geometry. The shield material should not be prone to warping when in contact with moisture.
Metal
Metal is a suitable material for strip foundation formwork. But it is used mainly in professional construction, since it is quite expensive. For the assembly of forms, sheet metal with a thickness of up to 2 mm is used.
This material allows you to make shapes of complex configurations, for example, semicircular. Metal formwork can be removable and non-removable. In the latter case, the reinforcement is welded to the formwork, which increases the strength of the structure.
Reinforced concrete
The use of reinforced concrete slabs for formwork under the foundation also requires additional financial costs. Depending on the thickness of the slabs, the amount of concrete can be reduced when pouring.
The presence of a stationary reinforced concrete formwork will allow maintaining the strength characteristics of the cast structure even with a decrease in the thickness of the main part. The disadvantage of this option is the impressive weight of the plates, which makes it necessary to use lifting equipment.
Expanded polystyrene
Foam permanent formwork for strip foundations is a practical option. Molds are assembled quickly because they are lightweight and easy to move by hand. In addition, this material perfectly serves as a heat insulator.
The disadvantages include not impeccability from the point of view of ecology, nevertheless, expanded polystyrene is a material of artificial origin. Another significant negative point is that the material, when heated, emits toxic substances, which is extremely dangerous in case of fire.
Wood
When planning to make do-it-yourself formwork for the foundation, many choose wood as a material. It is an affordable and easy-to-process material. Shields are hammered from the boards and timber, then it will be necessary to seal the cracks and prepare the spacers.
Movable formwork is made of wood; this material is unsuitable for creating permanent forms.
Materials at hand
For the manufacture of formwork for the strip foundation with your own hands, improvised materials can also be used. As a rule, sheet material is used. For example, professional sheet or slate. The only advantage of such a solution is its low cost, but there are many disadvantages, in particular, these are:
- the complexity of the assembly, it is not at all easy to fasten the slate sheets together;
- low indicators of load resistance;
- the need to install a large number of additional spacers.
What is the formwork for the foundation: the main varieties
Depending on what materials are used and what shape the structure takes, the formwork can have different properties.There are several varieties that should be studied before starting construction.
When building two or three houses, the formwork can have a completely different look.
If possible dismantling
The main principle that must be followed when creating the formwork is the possibility of subsequent dismantling. The design can be:
- non-removable, that is, it is part of the foundation and is not removed from it. This allows you to improve the performance and increase the thermal insulation of the future building. A suitable material for such formwork is expanded polystyrene;
- collapsible, in this case, dismantling is carried out after the concrete is half dry. You can use the same formwork several times, which is very convenient for the construction of residential complexes. The number of fillings required depends on the material used to create the structure. Most often, three to eight cycles are sufficient.
It is recommended to use the removable formwork several times in order not to transfer the material
By materials of manufacture
In order to create the formwork, you need to use the following materials:
- wood boards;
- metal blanks;
- reinforced concrete;
- expanded polystyrene.
The most expensive option is metal. Steel sheets with a thickness of 1 millimeter or more are used, which are necessarily mounted when creating a strip or monolithic foundation. If necessary, you can create a structure of any configuration. If there is a need to increase the rigidity of the material from which the base is made, the reinforcement should be welded to the metal sheets.
Metal processing is very expensive
Another, no less expensive option is the manufacture of reinforced concrete formwork. To form it, ready-made concrete sheets are used. This method allows you to create a reliable structure, while reducing the consumption of concrete mortar. To carry out the installation, you will need special construction equipment.
If one plate is not enough, additional materials and spacers must be used. In this case, the cost of work will be increased.
The use of reinforced concrete formwork reduces the amount of liquid concrete and simplifies the workflow
Also quite practical and high-quality is the construction of expanded polystyrene, for the creation of which blocks are used. There are no difficulties during installation, however, when creating corners and fillets, you need to prepare the blocks in advance and follow the instructions.
You do not need to have special skills to install polystyrene foam.
If funds are very limited, it is recommended to use wooden formwork. To create it, they use ordinary boards or plywood, which are inexpensive. To create a structure, it is enough to use just one construction tool for carpentry work. However, due to the fact that such a structure needs to be further strengthened, the costs can ultimately increase dramatically.
Wood formwork is the most common option today