Instructions for gluing a car bumper with your own hands
When starting to repair a bumper, you need to perform a number of steps step by step. Compliance with the instructions will help to avoid common mistakes and achieve the desired result with a minimum of time and effort. The basic bonding process consists of preparation, joining parts and work to restore the appearance.
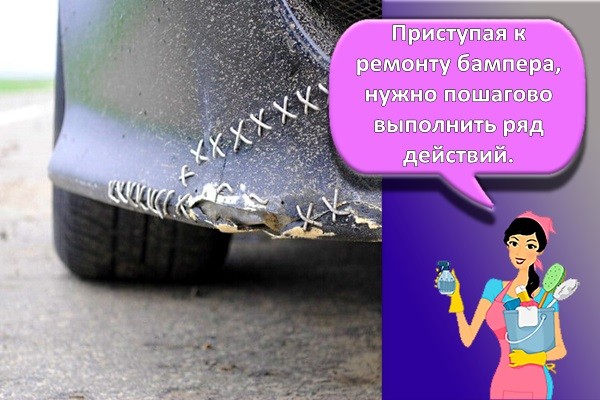
Preparatory work
The initial stage of repair is to prepare the working surface. The bumper is inspected, washed from accumulated dirt, the edges and edges are treated with an abrasive material or a cutter. Then, with the help of special chemicals, degreasing is carried out.
Bonding cracks on the bumper of a car
When gluing cracks on a cracked bumper, it is necessary that the amount of adhesive solution on the parts is optimal. Insufficient thickness of the adhesive layer will lead to the fact that after the solution dries, the materials will not obtain identical physical characteristics. Differences in rigidity lead to the destruction of the paintwork after all work is completed, even with a slight external impact.
The glue is applied in an even layer on two parts, which will be connected to each other. To strengthen the seam from the inside, the crack can be sealed with a metal or synthetic mesh. The final hardening of the solution occurs over a different period of time, depending on the characteristics of the substance. To prevent the parts from moving after gluing, you must first ensure that they are securely fixed in place, and carry out the work without removing additional fasteners.
v class = 'code-block code-block-12' style = 'margin: 8px 0; clear: both; '>
Priming and painting
After gluing the damaged bumper, it remains to carry out the final work to restore the proper appearance of the part. First of all, for the restoration, the excessively applied amount of material is removed by cutting or processing with a grinder. Then the entire surface of the bumper is cleaned and the resulting irregularities are removed, using a putty if necessary.
Having leveled the surface of the bumper, proceed to painting the part. The procedure is carried out in accordance with the standard plastic painting technology. In this case, it is allowed to use enamel and paint in work that are not intended for plastic, but in this case, you will need to add a plasticizer. To give the surface of your car bumper a rougher finish, it is best to use a structural paint. If the task is to paint the bumper in body color, then you must first apply another additional layer of primer, and then proceed to painting.
Share link:
How to glue at home
The strength of the connection of materials depends not only on the quality of the purchased glue, but also on the condition of the base. The latter is recommended to be degreased and cleaned of dirt before starting work.
Preparing the base for bonding
Each base must be cleaned of dirt, rust and moisture before gluing. The metal must be wiped with a choice:
- acetone;
- white spirit;
- alcohol (vodka).
These fluids remove grease, thereby increasing the adhesion of the material. The glass should be cleaned with a suitable detergent and dried. If there are traces of paint or varnish on the metal, these materials should be removed with a grinder or sandpaper. After the procedure, the base should also be degreased.
Stages of work
To reliably glue glass and iron, it is necessary to warm up both components to 40-50 degrees. For this, it is recommended to use a building hair dryer. On contact with an open flame, the glass cracks.When heated, the remaining moisture is removed, thereby increasing the level of adhesion of materials.
After that, you need to apply glue to the parts and level the composition, forming a thin layer. Then the components should be folded together and pressed tightly under the press. It is recommended that escaping adhesive be removed immediately. Otherwise, noticeable stains will remain on the processed materials in the future.
UV lamp application
Under the influence of ultraviolet radiation, the strength of the seam increases. Before gluing, the parts should be heated to 60 degrees. After connecting the components along the seam, you need to run the ultraviolet lamp twice. After the initial exposure, the level of strength of the adhesive composition increases by 70%, after the second - by 100%.
What varieties are suitable
The range of adhesives is extensive. But for working with glass and metal, a limited list of such compositions is suitable. Polyurethane, cyanoacrylate, silicone and a number of other adhesives are suitable for joining products made of these materials.
Two-component epoxy
Polyurethane adhesives, depending on the type of ingredients included in the composition, are divided into one- and two-component. The first variety is relatively popular, since it does not require preliminary preparation and dilution of the constituents of the material.
These compounds provide a strong connection, but harden more slowly than the first, so that, if necessary, the parts to be fastened can be more accurately applied. Such adhesives contain resin and active substances that determine the degree of viscosity, drying rate and other characteristics.
Silicone heat resistant
Silicone heat-resistant adhesives are used to repair glass that is constantly exposed to high temperatures. This includes materials used in ovens and other similar household appliances. The heat resistance of the adhesive is provided by individual components that are added to the initial mixture.
The disadvantage of silicone is that it takes longer for the material to harden. But such sealants tolerate long-term contact with fat and oils, exposure to negative temperatures well.
Moment Crystal
This product is suitable for gluing:
- glass;
- porcelain;
- metals of different types;
- PVC;
- wood;
- plexiglass.
Moment The crystal is transparent and quickly solidifies. This product is not recommended for gluing objects that come into contact with food. Moment Crystal is suitable for creating seams that are exposed to increased stress.
Car
Automotive adhesives are characterized by increased adhesion and resistance to aggressive substances. This type of material creates transparent seams. Such compounds are also available in different colors, so you can glue any parts of the car. To create a strong seam, it is recommended to additionally warm up the joint.
Cyanoacrylate
Cyanoacrylate, depending on the type of ingredients included in the composition, can be one- or two-component. Both types of glue dry quickly: the seam hardens within 5-10 seconds. Some cyanoacrylates cannot withstand moisture
You should pay attention to this when buying
Sealant
High-quality sealants are not inferior to silicone heat-resistant adhesives. Such materials are also able to withstand sudden temperature changes (including up to +300 degrees), contact with water and fats. It will take at least a day to completely dry the sealant.
Varieties and labeling
Depending on the composition of the adhesive base and substrate, "Oracal" is subdivided into several types.
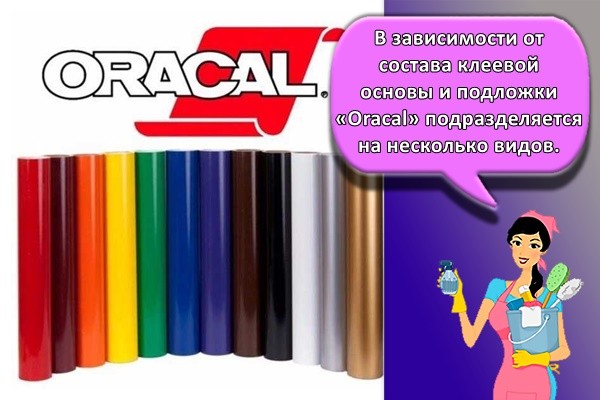
551
Oracal 551 is commonly used to transfer decals to vehicles. The palette of shades of such a film has 98 shades. At the same time, only white and black materials are matte.
620
Easily removable version of "Oracle" with a matte or glossy surface. This material is used for advertising purposes.
640 and 641
The film of this type is characterized by increased resistance to temperature extremes - from -40 to +80 degrees. The material does not fade in direct sunlight, therefore it is used to decorate the external walls of buildings. The color palette includes up to 60 shades.
951
The product tolerates extremely low (up to -80 degrees) and extremely high (up to +100 degrees) temperatures. In metallic color the film is produced in 49 shades, in the usual form - in 97. This material has a mirror-glossy shine, and therefore is often used for advertising purposes. The film is suitable for adhering to difficult and uneven surfaces.
970
Oracal 970 is used for wrapping vehicles, including sports cars. The film of this type can withstand a temperature drop of up to -50 degrees and an increase of up to +110. The product is resistant to alkali, engine oil and other automotive lubricants. Oracal 970 is produced in white, black and yellow colors.

8300 and 8510
Oracal 8300 and 8510 are available in 32 shades. The material is used to decorate shop windows and illuminated stained glass windows. The film is characterized by increased strength and changes colors when several layers are applied.
6510 fluorescent
The material with a semi-glossy surface is illuminated at night due to specialized processing. Because of this, the film is created in a limited color palette. Oracal 6510 is available in only six shades. Like the previous one, this type of product is used for advertising purposes.
How to glue correctly
When gluing Oracal, a number of conditions must be met. At temperatures below 10 degrees, the material loses its original properties, therefore it is not suitable for use. If the film is glued at +30 or more, then the product becomes plastic, which complicates the application to the surface.
Surface preparation
It is recommended to glue "Oracal" onto flat and previously degreased surfaces without contamination. For this, the place of future work is washed with soapy water. Depending on the type of surface, the following procedures may be required:
- putty on irregularities and cracks;
- varnishing (for wood);
- primer treatment (for rough surfaces);
- processing with a solution with dishwashing detergent (for glass, metal and other smooth surfaces).
The described procedures help to achieve the strongest possible adhesion of the material to the surface.
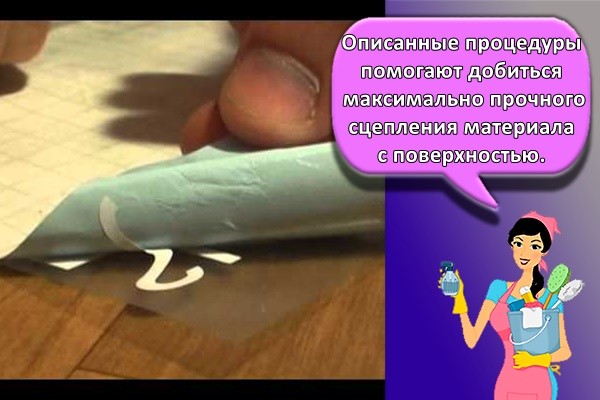
Sticking
To stick "Oracal", you need to separate no more than 5-7 centimeters of the protective film and apply the material to the surface, smoothing all the irregularities with your hand. The last procedure must be carried out moving from the center to the edges. If bubbles form, such defects can be removed by puncturing with a needle.
The rest of the material is glued according to the same scenario: first, 5-7 centimeters of the protective film are removed, and then the self-adhesive is leveled. If it becomes necessary to apply a product on an uneven surface with corners and deep grooves, then "Oracal" in these places must first be warmed up with a hairdryer. Under the influence of temperature, the material becomes more malleable.
Alignment
As noted, it is necessary to align from the center to the edge. It is necessary to smooth the material several times, eliminating, among other things, minor defects. The degree of adhesion of the adhesive base to the surface depends on this.
How to lubricate the caliper
Caliper products are mainly made on a copper or ceramic base. The composition may include mineral, semi-synthetic and synthetic oils.
Molykote Cu-7439 Plus
Molykote Cu-7439 Plus is made from fine copper powder. The paste can be used with the calipers of the auto giants Land Rover, Honda, Subaru, Nissan. Molykote Cu-7439 has many advantages - the video tells about them:
MS-1600
MC-1600 is the best domestic paste. It has a wide operating temperature range - from -50 ° C to 1000 ° C. MS-1600 does not enter into chemical reaction with TZ DOT 3, DOT 4, DOT 5.1.Interacts with DOT 5.0.

XADO VeryLube
XADO VeryLube is a green spray with the article number XB40019. You need to apply it in layers. Each layer should be kept until it is completely dry. The standard 320 ml capacity is enough to handle all car calipers.
SLIPKOTE 220-R DBC
The best antiwear and antioxidant properties are possessed by a product based on a synthetic refined oil - SLIPKOTE 220-R DBC. It is used with the brakes of many new cars. In retail, SLIPKOTE 220-R DBC can be found in Toyota packaging with the article number 0888780609.
Suitable types of glue
In practice, adhesives are most often used, which include polychloroprene or polyurethane.
Polychloroprene based
Polychloroprene adhesives contain solvents, resins or metal oxides to increase bond strength and resistance to temperature changes. During the gluing process, local heating with a hairdryer may be recommended, which accelerates the polymerization and gives a strong bond. After the completion of the constriction, the car is ready for use in 30 minutes.
Popular brands of adhesives:
- "Clay-88". Advantages: suitable for all types of cladding, resistant to high humidity. Disadvantages: poor hold, toxic odor during work.
- GTA Boterm. Advantages - resistance to temperature fluctuations, high humidity. To activate the connection, heating up to 60 degrees is required.
- "Mah." Forms a good connection, heat and moisture resistant. The disadvantage is the high cost.
- Kaiflex K414. One component UV resistant compound. The strength of the joint is achieved through the effect of cold welding.
Expensive brands of adhesives are used by professionals.
Polyurethane
Polyurethane adhesives belong to the category of universal ones, they give a strong fixation of the base and material. Drying time allows you to correct the defects of the constriction. Grades of polyurethane-based adhesives used in ceiling panel hauling:
- "Moment". For constriction use universal varieties - "Moment Crystal" and "Moment-1". Adhesives have good adhesion, moisture resistance, withstand temperatures from -40 to +100 degrees.
- "Titan" ("Titan"). Specialized glue, has a viscous consistency, quickly sets. The composition gives a strong connection, is non-toxic, colorless, retains properties from -30 to +60 degrees, moisture resistant.
- "Demoskol". Colorless, stable in a humid environment, withstands mechanical and thermal stress.
Polyurethane adhesives are produced ready-made in convenient packaging.
Alternative options
For the decoration of car dealerships, aerosol adhesives are used. Advantages of adhesives:
- economical;
- do not spread;
- do not leave traces;
- give an even coating.
The disadvantage is the high cost, the mandatory availability of skills in application due to the high drying rate.
Why lubricate brake pads and is it really necessary?
All elements and functional units of the brake system require special care. This is due to the fact that during heavy braking, the temperature there can reach 600 degrees Celsius or higher. At the same time, during cooling, the decrease in the temperature index can also be quite sharp - up to 180 degrees. Another of the negative influences can be distinguished such as the effects of corrosion and dirt, all kinds of chemical compounds. In simple terms, the conditions are extremely harsh and any method is suitable to provide additional protection.
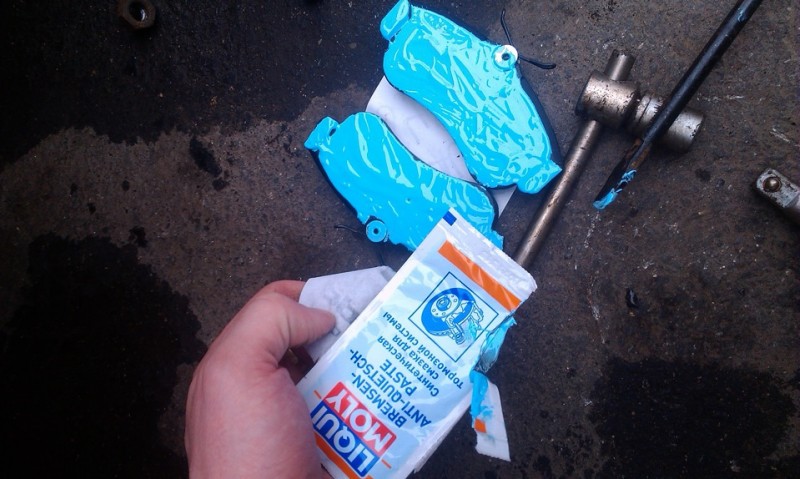
For protection, specialists use special lubricants that are applied to parts during repairs or during a technical check of the brake system. In order to guarantee the protection of the mechanisms, it is worth taking a very responsible approach to finding a suitable lubricant. For more information on lubricants, see the video:
Basic requirements for the adhesive
Glass has three qualities that interfere with the adhesion of parts made of this material:
- low adhesion;
- increased fragility;
- transparency.
Adhesives used to join glass products must create not only a strong, but also a transparent seam. Otherwise, the hitch point will be noticeable against the background of the material. However, not only these qualities should characterize the selected adhesive. For glass and metal, it is recommended to select a composition with the following properties:
- viscous;
- sets quickly;
- resistant to temperature extremes and high humidity;
- safe for humans;
- elastic.
Such qualities are characteristic of expensive adhesives. But it is not recommended to save on such materials.
Strength
This indicator is considered the most important. The durability of the joint created depends on the strength of the bond. For glass, it is recommended to buy adhesives that adhere tightly to parts when exposed to ultraviolet radiation. The joints obtained in this way are able to withstand increased loads.
Tightness and moisture resistance
Some glass and metal products often come into contact with water. Therefore, for gluing such materials, it is recommended to buy adhesives that have the properties of a sealant.
Solidification rate
This parameter does not play a decisive role. However, the cure rate of the adhesive should be considered when choosing a product. Fast-drying materials harden in a matter of seconds, which is why it is necessary to immediately accurately connect the glass parts to each other.
What is brake lubricant for?
The result of applying brake grease depends on the area of application. The coating of the guides in the wells of the caliper brackets leads to an increase in the smoothness of the movement, a decrease in wear, a decrease in the risk of jamming and the appearance of scoring.
There are tools to help eliminate high frequency squeaks. They help to reduce extraneous noise during braking. Also anti-squeak pastes protect against corrosion.
To facilitate disassembly, formulations are used to prevent adhesion of parts. They have a copper or nickel base and have anti-squeak properties.
Lubricating the seating surfaces facilitates assembly of the calipers. At the same time, the use of special means to simplify the installation of pistons into cylinders helps to reduce the risk of corrosion.
Review of popular brands
When repairing friction linings, motorists most often prefer 3 adhesives.
"VS-10T"
The glue is made up of special resins and organic solvents. The parts to be glued are first removed to the side until completely dry, only then they are installed under the press. By its appearance "VS-10T" is a viscous homogeneous transparent liquid of beige or brown shade. This glue does not contain water, which makes it stable, even in case of direct contact with liquid. Also, the composition is resistant to most aggressive environments: sea water, alcohol-containing liquids, acetone.
The VS-10T glue is specially designed for reliable fixation of materials in units that operate at temperatures up to 300 ˚С. It can be used at low pressure. The adhesive is widely used for bonding brake linings to a metal backing. The composition guarantees high adhesion strength.
Poxipol
Two-component, high-strength, all-purpose epoxy adhesive. Its main purpose is assembly and construction work, but the composition of "Poxipol" has proven itself well in gluing and repairing various mechanisms. After working with it, a seam forms on the surface. For this tool received a second name - "cold welding".
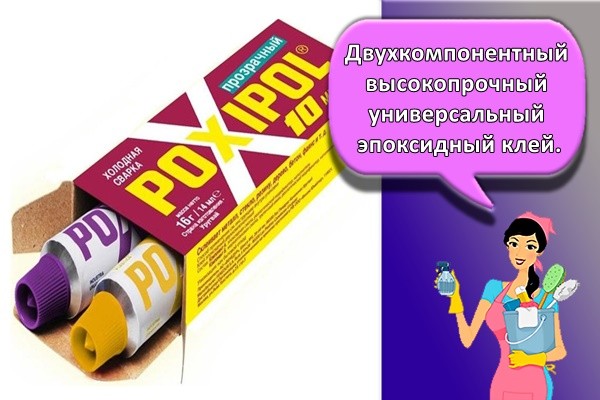
Glue is sold in a set of 2 tubes:
- in a tube marked "A" - resin;
- in the second, with the designation "B" - hardener.
The kit also includes instructions for use, a spatula, a plate. The resin has high flexibility, guarantees increased adhesion of parts. The acceptable temperature for gluing is + 18 ... + 23 ˚С.
The disadvantages of the adhesive include:
- Poxipol is not suitable for working with polypropylene, polyethylene, Teflon;
- high product cost;
- before applying the composition, it must first be prepared, and then used within 5-6 minutes.
Natural glue is sold only in specialized stores.
Epoxy resin "ED-20"
Epoxy-diane resin is a reliable universal viscous liquid of high quality without mechanical impurities. Under the influence of a hardener, at normal room temperature + 20˚C, it turns into an infusible polymer.
Technical characteristics of the composition:
- shows resistance to moisture, mechanical damage, alkaline, acidic environment;
- the prepared mixture is used within 30-60 minutes;
- when compared with acrylic resins, it is toxic;
- low elasticity - in the process of movement on the surface, which is covered with "ED-20", cracks may form;
- has anti-corrosion and dielectric properties;
- provides high durability under heavy loads.
In industry it is used in its pure form. Without additional components of the composition "ED-20" amber or orange color.

Semi-Metallic Pads
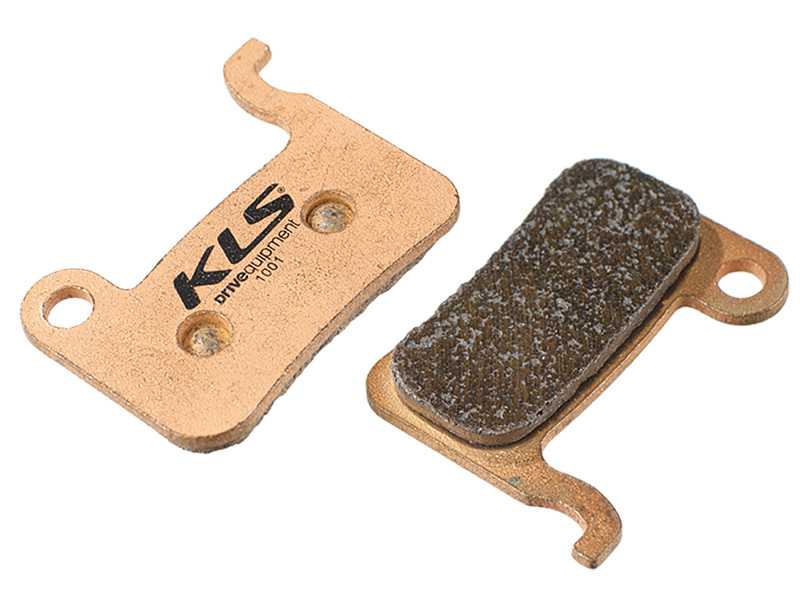
The composition of the friction clutch here does not differ from organic, but
the quantitative composition has been changed - up to 65% of metal inclusions are allowed. They
all are also immersed in a special heat-resistant resin or other binder.
Characteristics
Traditionally, it is believed that semi-metallic pads
are a compromise between organic and inorganic. They have merit
of one kind and are devoid of the shortcomings of the other. In particular, they:
They are less noisy than inorganic, but at the same time they have
better modulation.
They brake more efficiently than sintered pads, but
wear out more slowly than organic ones.
They rub in faster.
They work with all types of rotors, except
frank rotors-saws.
Adequately respond to changes in weather
conditions.
You need to ignite with great care.
Types of lubricants for brake pads
Sometimes figuring out the best way to lubricate the brake pads is not easy. This is due to the fact that the range of such products is very wide, and it is difficult for beginners to choose a composition that will satisfy all the characteristics and parameters of a particular brake system.
In this case, I would advise you to first pay attention to the following characteristics:
- what substances and elements are included in the lubricant;
- specific features of the offered products;
- brand name and cost of the composition.
It is possible that these criteria allow you to select the most suitable product for pads lubrication. In addition, it is worth talking about the classification of lubricants, taking into account the composition.
Options |
Synthetics and "mineral water" with metal microparticles |
Mineral emulsions |
Synthetic oil based lubricants |
general description |
Products capable of retaining their properties even at high temperatures. The composition includes synthetics and minerals with the addition of metals. |
Bentonite is added to the lubricants, which acts as a thickener, as a result of which a special emulsion is obtained. Not suitable for operating conditions of the mechanism, where there is rapid braking and aggressive external influences. |
A very popular and demanded lubricant in the form of a paste. Used for particularly difficult operating conditions. |
Application features |
Temperature range: -185 - 1100 degrees Celsius. |
Works at -45 - + 180 degrees Celsius. |
Withstands from - 40 to + 300 degrees Celsius. |
As practice shows, the compositions from the latter group are distinguished by the greatest stability and the ability to provide the unit with special protection.
The choice of ceiling fabric for constriction
The material for the headlining must correspond externally to the interior upholstery of the passenger compartment. For example, eco-leather will be combined with natural leather, flock - with velor. For homogeneous materials, the main thing is to choose exactly or one tone lighter trim for the ceiling.
Flock
The material resembles velor in appearance, but is much cheaper and more practical. Artificial material is obtained by gluing chopped fibers from wool, cotton, synthetics onto a base cloth. Mixed and polyester flock is used to stretch the ceiling in the passenger compartment.

The composition of the mixed flock includes: nylon (pile), cotton with synthetics (base). Polyester flock is similar in properties to the mixed one, with the exception of the color range (available only in black). Flock is the most demanded material for covering car dealerships. Causes:
The peculiarity of the use of upholstery material is the prohibition of the use of cleaning agents containing alcohol, acetone. We recommend the use of special products to avoid the build-up of static electricity.
Eco leather
Eco-leather differs from leatherette in higher quality. The material consists of 2 layers: polyurethane (natural leather texture) and cotton / polyester (base). Polyurethane is a durable, non-toxic, breathable polymer. Dyeing and embossing give it a natural leather look.
The advantages of eco-leather are:
- in elasticity that prevents tears;
- a wide range of colors and textures;
- hypoallergenic;
- incombustibility;
- dirt-, water-repellent properties;
- preservation of colors under the influence of sunlight;
- resistance to temperatures up to -40 degrees;
- availability in processing.
Disadvantages of the material in comparison with other covering fabrics:
- mechanical damage leads to disrepair (loss of attractive appearance);
- not maintainability when the polyurethane layer is destroyed;
- heats up in the sun.
When cleaning the coating, do not use metal brushes and abrasives, products containing chlorine.
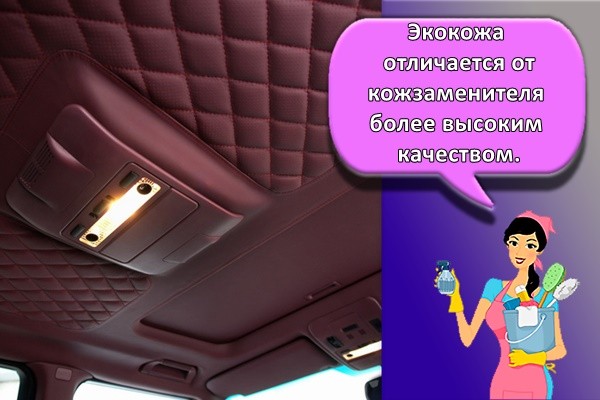
Leather
For car dealerships, special auto leather is used, which is stronger and more expensive than leather for shoes and clothes. Genuine auto leather is an expensive material used in premium models. Unlike artificial surfaces, it has a number of significant disadvantages:
- has a high thermal conductivity (the ability to heat up and cool down strongly);
- poorly breathable;
- difficulty in leaving.
The main advantage of natural material is prestige for the owner.
Alcantara
Alcantara is of two types: Italian and self-adhesive. The Italian material has textiles or foam rubber on the seamy side. Self-adhesive Alcantara has an adhesive base. The material is specially designed for the decoration of car dealerships. The fabric looks and feels like suede (with self-adhesive the pile is longer) and has the following characteristics:
- moisture resistant;
- easily cleaned of dirt;
- fireproof;
- does not fade in the sun;
- does not darken in the cold;
- does not crack from temperature changes;
- wear-resistant.
The material is available in a wide range of colors.
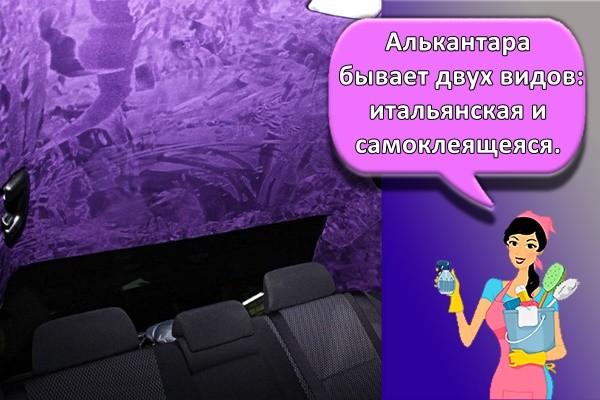
Carpet
Carpet (carpets) is available in three modifications, determined by the length of the pile:
- The pile is missing. Dense, soft, elastic fabric.
- Pile length - 6 millimeters (tufted carpet).
- Pile length - 10 millimeters (premium material).
Advantages of synthetic fabric:
- resistance to moisture, high temperature, UV radiation;
- not electrified;
- not toxic;
- wear-resistant.
Feature of application: you can not use hot melt adhesives, which require heating over 50 degrees.
What to lubricate when replacing brake pads
When replacing the front or rear brake pads, apply lubricant to the caliper rails. This will protect them from acidification, deformation, corrosion, and also reduce mechanical wear. If the vehicle is equipped with an ATE open rail braking system, do not apply special equipment.
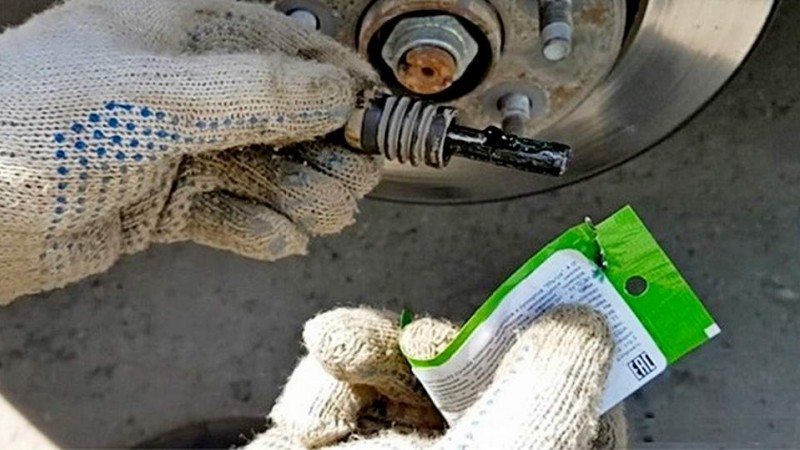
To reduce high frequency sound, apply a thin layer of paste between the plate and the non-working side of the pad. It is recommended to cover the ends of the consumable with a special tool. This prevents the pad from rubbing against the caliper. It is forbidden to use block grease for the guides - the rubber boots will swell. The tightness will be lost, moisture will get inside, the corrosion process will take place.
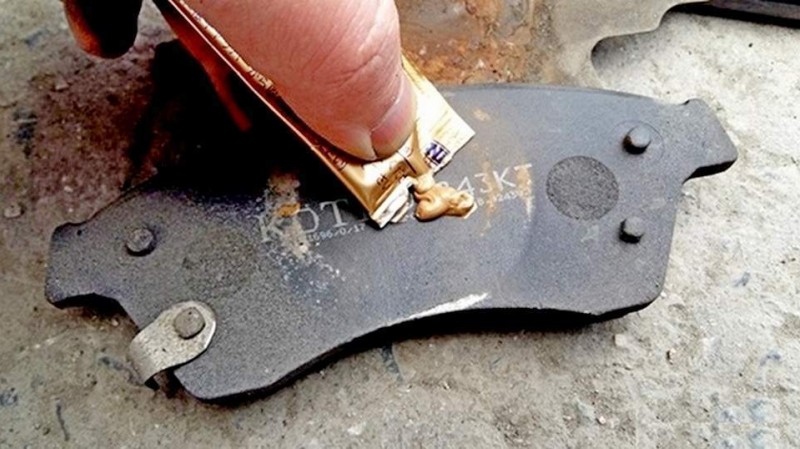
When replacing brake pads, grease is also applied to the plates holding them. It allows you to reduce the volume of extraneous sounds and protects against rust. It is worth applying the paste not only to the staples, but also to the seats.

For reliable operation of disc brakes, it is recommended to lubricate the piston. This will allow it to move freely inside the cylinder.
It is important that the compound does not react with brake fluid. In more detail, the effect of TJ on lubrication is discussed in the video:
It is not necessary to remove the piston to apply the product.
There is a high risk of rupture of the cuff, therefore, when servicing the unit, it is important to correlate the risk of damage to the boot and the need to change the lubricant on the piston. In the absence of the necessary skills, it is better to contact a car service.
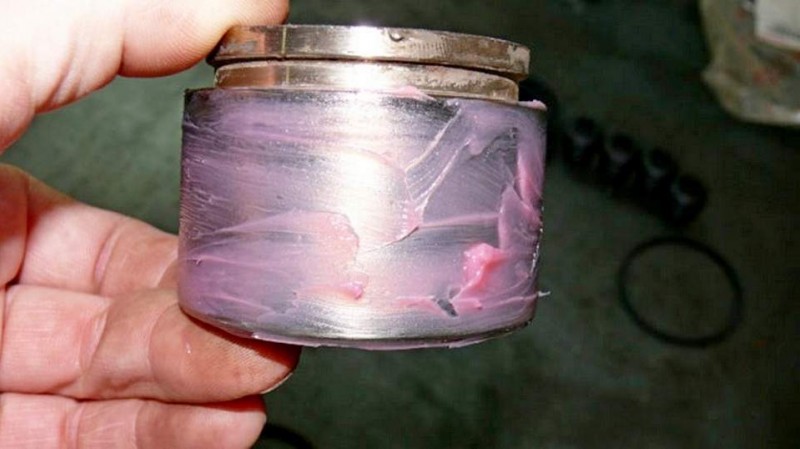
Treat fasteners with special means. Then it will be easier to disassemble the mechanism. To prevent spontaneous loosening or damage to the thread, it is necessary to control the tightening torque with a torque wrench.
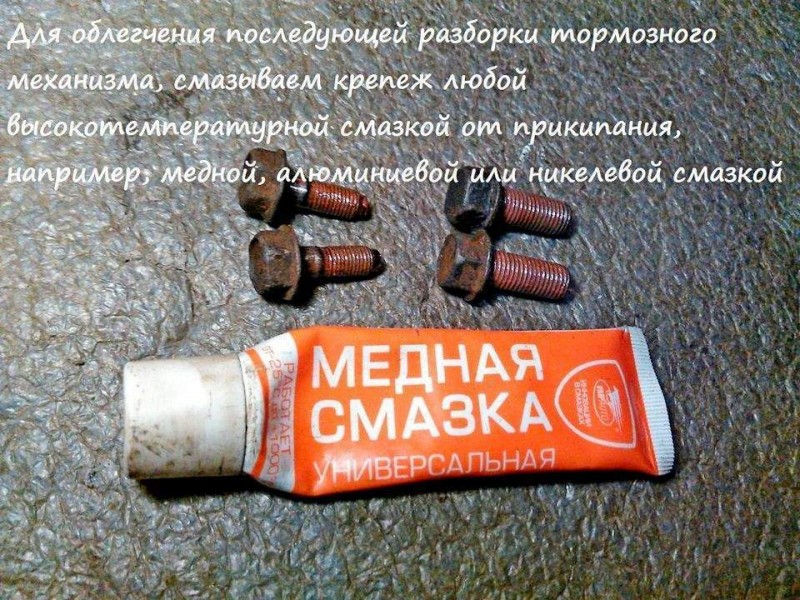
If replacing the pads involves installing a new disc, the surface underneath should be covered with an anti-stick agent. Copper grease in aerosol cans will do. The spray torch must be guided carefully so that liquid does not spill onto rubber or plastic surfaces.
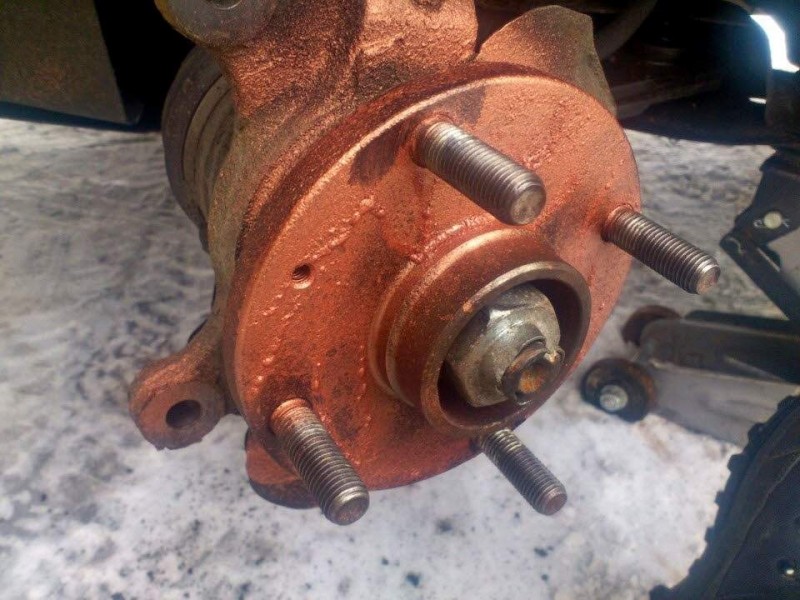
Conclusion
We have seen the main types of bicycle pads for
disc brakes and their features. Each type of pad has its own
advantages and disadvantages. Of course, each type has both fans and
haters. Which one to prefer you need to decide on your own.
There is no definite answer to this question - some pads behave well in one
situation and others in another.
The trade-off between these characteristics is only yours.
a choice that should be based on personal preference and common sense.
In practice, it often happens
it is convenient to use one type of pad on one wheel and the other on the other.
So, sometimes it is very convenient to install sintered metal pads on the rear
brake, so more dirt gets on it and the load is higher there, and on the front
put organics.
It is useful to try using both one type of pads and
another, but on the basis of personal experience to make a final conclusion.